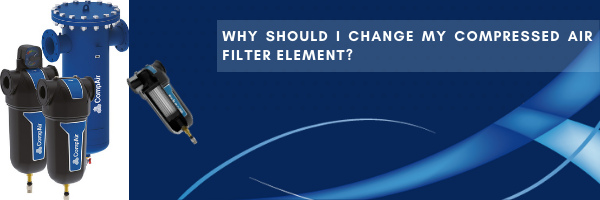
Over 90% of manufacturing facilities world-wide use compressed air as part of their manufacturing process. However, this powerful utility is not without its problems, in the form of compressed air contamination. It is therefore common practice to install compressed air filters as part of a “purification system” to ensure contaminants are reduced and the system operates in a safe, efficient and cost effective manner.
Compressed air filters function under extremely arduous conditions.
- Pressure variations
- Pulsing air demand
- Temperature variations – Day / Night & Summer to Winter
- High / Low Humidity – From 100% saturated air to extremely low dew point’s
- Chemical attack – from oily acidic condensate and lubricant additives
Coalescing filters are constantly soaked in oily, acidic condensate, whilst at the other end of the spectrum, dry particulate filters operate in very low humidity which over time, weakens and degrades the strength of the filter media. When the filter is operating, the filtration media in the filter element is bombarded by high-velocity dirt particles. This constant bombardment will eventually lead to weakening and failure of the filter media. Once the filtration media becomes damaged, the required air quality can no longer be maintained or guaranteed. Filter elements therefore have a finite operating life.
What Happens to The Filtration Media in A Filter Element If It Gets Damaged?
Even a tiny hole the size of a pin-point can have disastrous consequences. Compressed air will always take the path of least resistance and once the filter media is damaged the compressed air will force through the media, tearing and rupturing the length of the element. This will result in all of the contamination being carried downstream.
Pressure Spikes
Large pressure differentials or “pressure spikes” can also rupture filter elements in an instant, again, allowing contamination to be carried past the filter and into the compressed air system. When pressurizing systems (or the filter after servicing), always ensure isolation valves are opened slowly to prevent damage.
So When Should Filter Elements Be Replaced?
The recommended replacement times are for the following CompAir filter ranges
Filter Types | Replacement Times |
Coalescing Filter | 12 months |
Coalescing Filter Float Drains | 12 months |
Dry Particulate Filters | 12 months |