The automotive industry has been influential to the economic growth of Pakistan, thanks to the production and sales of diverse types of vehicles and related services. This industry is also one of the biggest employers in the Pakistan, providing millions with jobs — many of the jobs performed are made simpler with the use of air compressors. In fact, some industry sectors, including vehicle repair facilities and auto body shops, have come to heavily rely on compressed air for various daily operations.
Importance of Compressed Air for Automobile Paint
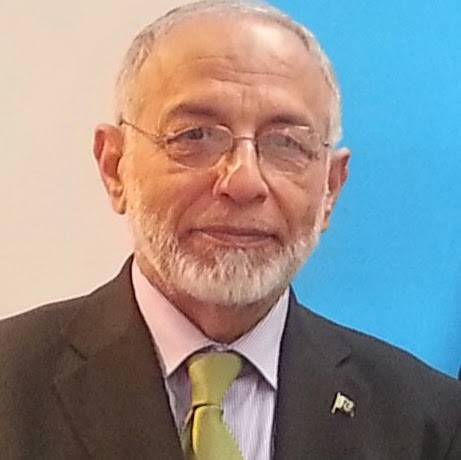
Auto body shops utilize compressed air for fast tire inflation and finishing services, such as painting. The compressed air is capable of vaporizing, and then propelling paint through paint guns or automated sprayers. Using this method, vehicles are given precision paint jobs in shorter amounts of time—without exposing workers to potentially hazardous materials. Additionally, most of the hand tools found in auto body shops run on compressed air. Air compressors are also very useful for handless tools; compressed air is used to power air-operated robots to assist in automated tasks, such as assembly, painting, structural repairing, and others.
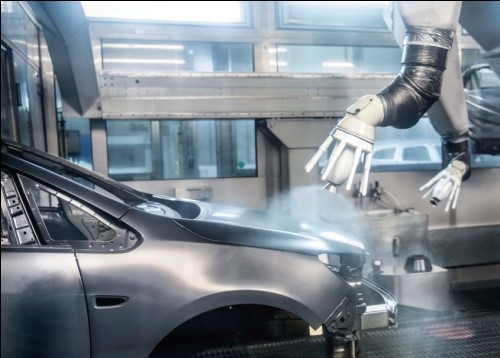
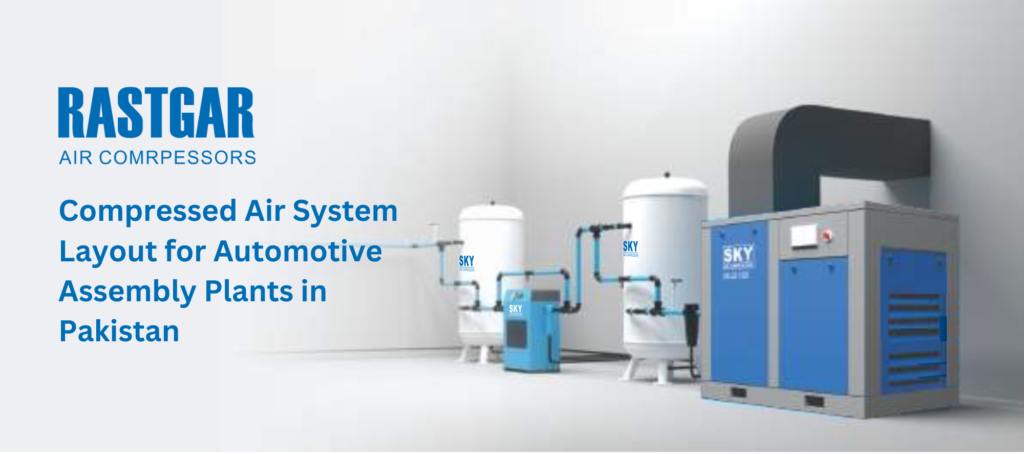
Oil-Free compressed air is critical to automotive assembly. Eliminating contaminants in surface preparation and painting processes helps ensure high quality final assembly.
Surface Preparation
Compressed air is used to clean and dry metal surfaces prior to painting. Oil contamination on these surfaces can impede paint adhesion and cause premature corrosion
Compressed air propels paint through paint guns and robots onto clean metal surfaces. For spraying the choice of compressor will depend on the air consumption and pressure requirement of the Spray Gun, and the number of spray guns used.
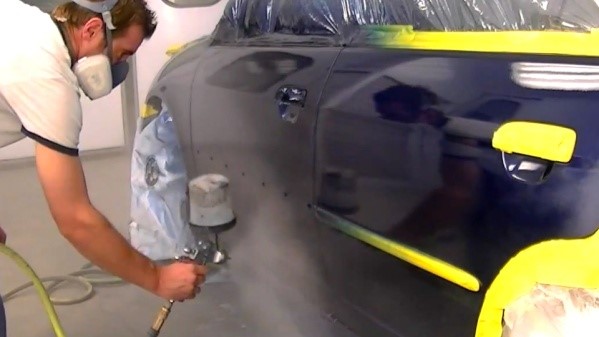
Compressed air agitates paint baths to mix the paint, maintain consistency throughout the bath and prevent coagulation.
Robot Operation
Compressed air powers vehicle assembly robots, which are sensitive to compressed air quality. These industrial workhorses produce virtually flawless paint finishes with superhuman consistency and throughput. Robotic painting is as much an art as it is science.
Water-based paints and silicones
Water-based paints are gaining popularity in the automotive industry in both spray and bath applications. Advances in performance and improved drying requirements have made water-based paints a viable solution for automotive manufacturers looking to significantly reduce their volatile organic carbon (VOC) emissions. In fact, many large manufacturers have converted entire plants from oil-based to water-based paints with the exception of clear topcoats.
While water-based paint durability has improved over the years, it is still very sensitive to silicones, which cause the paint to crack. Compressed air must be dry in order to prevent condensation downstream. Refrigerated air dryers are essential for producing air suitable for air tools, tire service, and paint spraying applications.
High quality filters are critical to removing contaminants such as dirt, rust, and oils common in compressed air. To reduce tool wear, promote quality paint finishes and reduce maintenance costs.
Bodyshop or automotive refinisher may be facing the challenge of switching to waterborne paints. These coatings have a reputation of being less tolerant of moisture and other contaminants, and many industry professionals say that the change to waterborne basecoats will require new equipment and retrofits. Unfortunately, specific technical specifications about compressed air requirements are hard to come by. Bodyshop or Automotive refinishers don’t want to compromise finish quality or waste time and materials re-doing paint jobs. They understand the value of a well-designed and reliable compressed air system and know the benefits of clean, dry air.
Filling cans is one of the ways compressed air is used by paint manufacturers. Stamping cans and transferring liquids are other uses. Air hoists are especially chosen in the presence of flammable varnish to handle varnish filters because of the absence of electric sparks
Choosing the right compressor for your needs and then properly setting up the system is vital. If the compressor is too small the type of gun and quality of finish can be affected. If the compressor is too large then unnecessary expense will be incurred. Using compressed air for spray painting gives greater versatility and the extra benefit of having the ability to operate other pneumatic equipment such as tyre inflators, chipping hammers, air blow gun, impact wrenches, ratchet wrenches, etc.
So many automotive industry professionals have already come to rely on compressed air to assist with day-to-day tasks — these operations would normally take much more time without it.
Rastgar Air Compressors, National brand of Pakistan in Compressed Air Systems, has been supplying auto industry with reliable compressed air systems which improves the overall performance of auto paint and body shops in many car assembly plants in Pakistan. Learn more
About Author:
Imtiaz Rastgar, an author and thought leader, graduated from the University of the Punjab and turned his passion for science, engineering and metallurgy into his business.
The company, Rastgar Engineering, which he founded in 1967 was exporting heavy axle parts to more than 70 countries by the time he retired from it. As a serial entrepreneur, he founded several other companies which are also running successfully within the engineering, manufacturing sphere.
He served as CEO and VP of the Engineering Development Board of Pakistan 2004-2007. His services were acquired by the Ministry of Foreign Affairs, CBI, The Netherlands as an Engineering Sector Expert 2007-2017.
Imtiaz Rastgar serves on the Board of Directors of Pakistan Aeronautical Complex, National Centre for Physics, Pak-Austria Fachhochschule Institute of Applied Sciences and Technology and several other seats of learning.
Now his consultancy and export marketing company PMX www.pmx.com.pk is available to all companies desiring to grow by going global.