Once you pick the right compressor, you next have to think about how to control it. It is very important to keep in mind that, while the efficiency of your compressor is the foundation for the efficiency of your entire compressed air network, there are other important factors as well. You can only get the most out of your system – and therefore enjoy maximum savings. Every 1 bar pressure reduction in the system reduces the energy consumption by about 7%. – if you select a control system that matches your needs. There are different methods of control – and once again it depends on the flow pattern to determine which one is best for you.
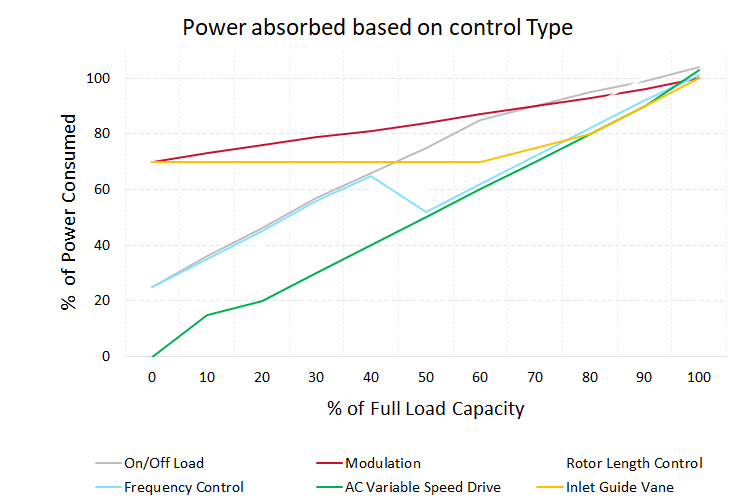
These methods range from very simple to highly sophisticated.
Some compressors are controlled simply by turning them on and off (start/stop). This control method is primarily used with smaller, fixed-speed models.
When using the load/unload control technology, the motor of the compressor runs continuously but it unloads the compressor once the discharge pressure is sufficient.
Another method, also used with fixed-speed compressors, controls the inlet valve and regulates the output of the compressor in that way. This method, called modulation, is very efficient for operations with a constant air demand.
When that demand varies, however, compressors equipped with a VSD (Variable speed drive), which controls the speed of the motor, are the best solution and offers the biggest savings.
Ideally, an operation would use a combination of compressors, for example fixed-speed models that meet the base load and VSD-equipped compressors that efficiently deal with fluctuations in air demand.
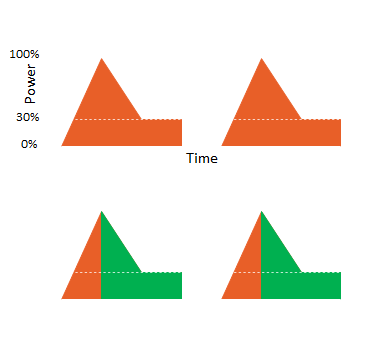
Picking the right controller
Advanced controllers like Delcos XL can help you manage your pressure and optimize your power consumption with smart algorithms designed to minimize power consumption.
The red line represents the power consumption of a compressor fitted with an on load off load controller. When the compressor is off loaded the power consumption is still 25 to 35% of the full load power. When the machine off loads it will run for a certain period before the motor stops. This off load timer prevents too many stops and starts.
A compressor fitted with an advanced controller can calculate the volume of air used by the speed of the pressure drop. It can then calculate when the compressor will need to go on load again. In periods of low demand, the controller can immediately stop the compressor to reduce off load power consumption. Saving energy while maintaining reliability
A compressor with a standard control and no timer feature will keep running during lunch breaks or even overnight when there are no production requirements. The compressor keeps operating wasting energy to feed air leaks.
A compressor fitted with multiple timers can be set to switch off during breaks and at certain times of the day when there is no air demand. Saving Energy.
With complete aftermarket support and service facilities all over Pakistan, Rastgar Air Compressors has been supplying Compressed Air solutions to the primary sectors of the manufacturing industry in Pakistan. Select an energy-efficient and reliable compressor for your facility.